Problemas Comunes en Calderas Tubos de Humo
- 22 may
- 5 Min. de lectura
Actualizado: 25 may

Termo Calderas ofrece un avanzado programa de mantenimiento para tu caldera y evitar los problemas mas comunes de las calderas Tubos de humo.
Las calderas de tubos de humo (también conocidas como pirotubulares) son equipos robustos, pero como cualquier maquinaria, presentan problemas comunes que pueden afectar su eficiencia, seguridad y vida útil. La mayoría de estas fallas están relacionadas con el tratamiento del agua de alimentación, la combustión y el mantenimiento inadecuado.
Aquí te presento los problemas más comunes en una caldera de tubos de humo:
1. Problemas relacionados con el agua (Lado agua):
Incrustaciones: Son depósitos adherentes que se forman en las superficies metálicas en contacto con el agua, principalmente en los tubos. Se producen por la precipitación de impurezas presentes en el agua a medida que esta se calienta y se convierte en vapor.
Causas: Agua de alimentación sin el tratamiento adecuado (alta dureza, sílice, etc.).
Consecuencias:
Reducción de la eficiencia térmica: Actúan como aislantes, dificultando la transferencia de calor del lado de los humos al agua, lo que aumenta el consumo de combustible.
Sobrecalentamiento de los tubos: Al no disiparse el calor correctamente, los tubos pueden alcanzar temperaturas excesivas, perdiendo resistencia y pudiendo colapsar, abombarse o romperse.
Mayores costos de mantenimiento: Requieren limpiezas químicas o mecánicas frecuentes.
Corrosión: El deterioro del metal debido a reacciones químicas o electroquímicas.
Corrosión por oxígeno (Pitting): El oxígeno disuelto en el agua reacciona con el metal, creando picaduras profundas y localizadas. Es muy común si el agua de alimentación no se desairea correctamente.
Corrosión cáustica: Se produce por concentraciones excesivas de sales alcalinas en zonas de alta carga térmica (hogar, placa trasera, cámara trasera). Crea cavidades profundas, a menudo rellenas de óxidos negros.
Corrosión por dióxido de carbono (CO2): El CO2 disuelto en el condensado forma ácido carbónico, que ataca las tuberías de retorno y el interior de la caldera, creando ranuras o canales.
Acumulación de óxido/hierro: El arrastre de óxido de las tuberías de la instalación de vapor o del retorno de condensado puede acumularse en el interior de la caldera, contribuyendo a la corrosión bajo depósito.
Consecuencias de la corrosión: Adelgazamiento de las paredes de los tubos, perforaciones, fugas, fallas estructurales y necesidad de reparaciones o reemplazos costosos.
Bajo nivel de agua: Es una de las fallas más críticas y peligrosas.
Causas: Fallo en el control de nivel, fugas, purgas excesivas, problemas en la bomba de alimentación.
Consecuencias: Sobrecalentamiento severo del hogar y los tubos, pudiendo provocar el hundimiento del hogar o el colapso/ruptura de los tubos debido a la pérdida de resistencia del material a altas temperaturas, con riesgo de explosión.
Formación de lodos: Las sales disueltas y los sólidos en suspensión en el agua pueden formar lodos que se depositan en el fondo de la caldera o dentro de los tubos.
Causas: Tratamiento de agua deficiente, purgas insuficientes.
Consecuencias: Obstrucción de la circulación de agua, sobrecalentamiento localizado y corrosión bajo depósito.
Arrastre de agua (Priming y Foaming): El agua de la caldera se arrastra junto con el vapor.
Foaming (Formación de espuma): Provocado por alta concentración de sólidos disueltos, alcalinidad excesiva o presencia de aceite/materia orgánica en el agua.
Priming (Arrastre súbito de agua): Puede ser causado por una demanda de vapor excesiva, un diseño de caldera inadecuado para la carga o una alta concentración de sólidos.
Consecuencias: Erosión de tuberías, válvulas y turbinas, contaminación del vapor, incrustaciones en equipos posteriores y menor eficiencia.
2. Problemas relacionados con la combustión y los gases (Lado fuego):
Acumulación de hollín y depósitos en los tubos de humos: El hollín es un subproducto de la combustión incompleta.
Causas: Combustión deficiente (mezcla aire-combustible incorrecta, quemador sucio o desajustado), tipo de combustible, operación con cargas bajas.
Consecuencias:
Reducción de la eficiencia térmica: El hollín actúa como aislante, impidiendo la transferencia de calor a los tubos.
Obstrucción de los tubos: Puede llegar a bloquear completamente el paso de los humos, reduciendo drásticamente el tiro y la capacidad de la caldera.
Corrosión por condensación de ácidos: Si los gases de combustión se enfrían por debajo de su punto de rocío, se pueden formar ácidos (como el sulfúrico) que corroen las superficies metálicas, especialmente en la parte trasera de la caldera o en la chimenea.
Riesgo de incendios: Los depósitos de hollín pueden encenderse si no se limpian regularmente.
Combustión deficiente o inadecuada:
Causas: Suministro de aire incorrecto, problemas en el quemador (piloto, encendedor, válvulas de gas), suciedad en los filtros de aire, chimenea obstruida.
Consecuencias: Baja eficiencia, mayor consumo de combustible, formación de hollín, producción de monóxido de carbono (peligroso), aumento de emisiones contaminantes y posibles fallos en el encendido.
Problemas con el refractario: El material refractario protege la carcasa metálica de la caldera del calor directo de la llama y los gases calientes.
Causas: Fatiga térmica, choque térmico, operación incorrecta, daño mecánico.
Consecuencias: Puntos calientes en la carcasa, pérdidas de calor por radiación, reducción de la eficiencia, daños estructurales en la caldera si no se repara.
Fugas de gases de combustión:
Causas: Daños en las uniones de los tubos con las placas tubulares, grietas en la carcasa, deterioro de las juntas.
Consecuencias: Pérdida de eficiencia, riesgo de entrada de gases tóxicos al área de operación, daño a otros componentes de la caldera.
3. Fallas estructurales y mecánicas:
Fugas en los tubos: Una de las fallas más comunes y problemáticas.
Causas: Corrosión (interna o externa), incrustaciones que causan sobrecalentamiento, fatiga térmica, erosión, defectos de material o mala instalación.
Consecuencias: Pérdida de presión, disminución de la eficiencia, arrastre de agua, daños a componentes eléctricos, riesgo de explosión si la fuga es grande.
Fatiga térmica: Se produce por ciclos repetidos de calentamiento y enfriamiento, o por diferencias de temperatura excesivas en diferentes partes de la caldera.
Causas: Arranques y paradas bruscos, operación con cargas fluctuantes, mala circulación de agua.
Consecuencias: Grietas en el metal, especialmente en las uniones y soldaduras, que pueden llevar a fugas o fallas catastróficas.
Deformación o colapso de tubos o hogar:
Causas: Sobrecalentamiento debido a incrustaciones, bajo nivel de agua, o mala circulación.
Consecuencias: Fugas, daños estructurales severos en la caldera, riesgo de explosión.
Problemas en las soldaduras: Las soldaduras son puntos críticos en la estructura de la caldera y pueden sufrir defectos de fabricación, fatiga o corrosión.
4. Problemas de control y seguridad:
Fallas en el control de nivel de agua (LWCO y ALWCO): Los interruptores de bajo nivel de agua son vitales para la seguridad.
Causas: Acumulación de sedimentos, corrosión, defectos eléctricos.
Consecuencias: No se apaga el quemador ante un bajo nivel de agua, lo que lleva a un sobrecalentamiento grave y riesgo de explosión.
Mal funcionamiento de válvulas de seguridad: No abren a la presión de ajuste o no cierran correctamente.
Causas: Corrosión, suciedad, ajuste incorrecto.
Consecuencias: Riesgo de sobrepresión y explosión, o pérdidas de vapor constantes.
Fallas en los controles de presión/temperatura: No regulan adecuadamente los parámetros de operación.
Causas: Sensores defectuosos, cableado suelto, desajustes.
Consecuencias: Operación ineficiente, sobrepresión o sobretemperatura, daños al equipo.
Problemas en el sistema de encendido o detector de llama:
Causas: Chispa débil, detector sucio o defectuoso, programador electrónico con fallas, válvulas de gas defectuosas.
Consecuencias: La caldera no enciende, o el quemador se apaga inesperadamente.
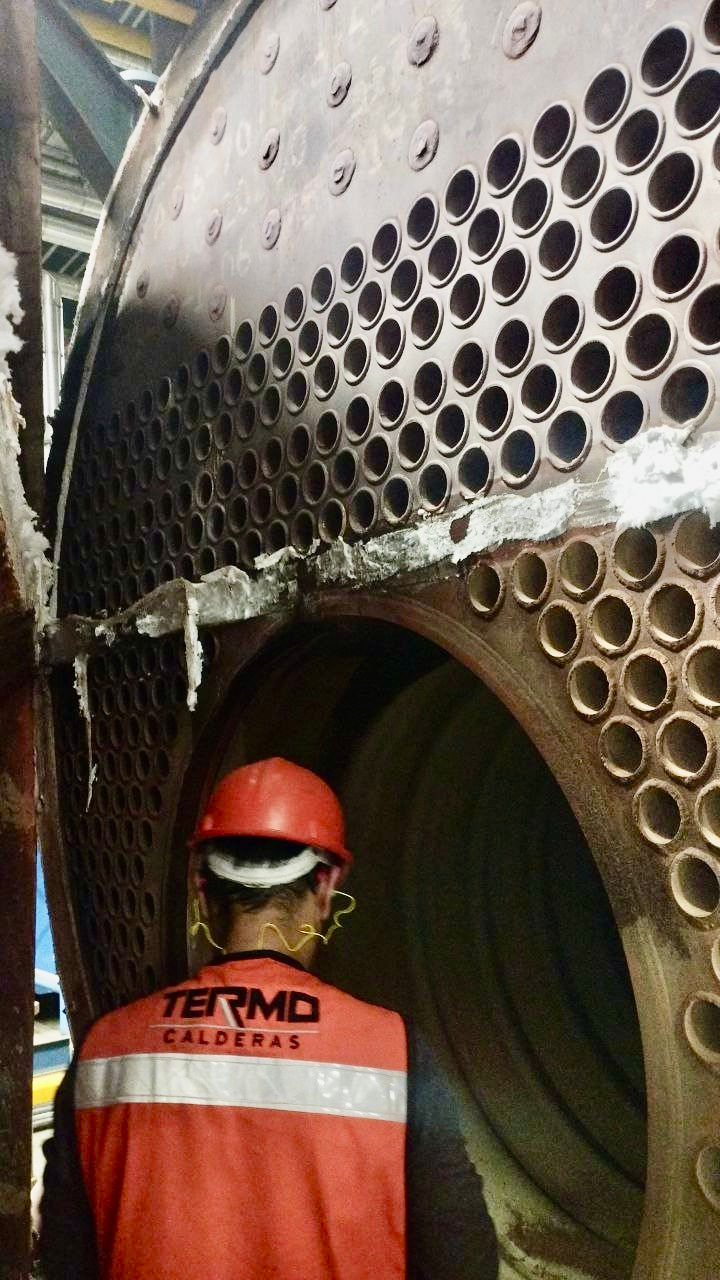
Prevención y Mantenimiento:
TERMO CALDERAS te ayuda a prevenir o mitigar estos problemas con nuestra poliza de mantenimiento preventivo que incluye:
Tratamiento de agua adecuado: Análisis constante del agua, dosificación de productos químicos, purgas regulares.
Limpieza regular: Limpieza del lado fuego (eliminar hollín) y del lado agua (eliminar incrustaciones y lodos).
Inspecciones visuales periódicas: Buscar signos de corrosión, fugas, deformaciones.
Pruebas de funcionamiento: Verificar controles de nivel, válvulas de seguridad, quemadores y sistemas de combustión.
Calibración de instrumentos: Asegurar que los medidores de presión, temperatura y controles funcionen correctamente.
Mantenimiento del refractario: Inspeccionar y reparar cualquier daño.
Capacitación del personal: Operadores calificados para identificar y responder a problemas.
Un monitoreo constante y un mantenimiento proactivo son clave para garantizar la seguridad, eficiencia y longevidad de una caldera de tubos de humo.
Comments